Diagnostyka olejowa – Zobacz, co Twój olej chce Ci powiedzieć …
Cykl, który otwiera niniejszy artykuł, ma na celu przybliżenie problematyki diagnostyki olejowej jako ważnego elementu strategii utrzymania ruchu. Diagnostyka olejowa zostanie przedstawiona od strony inżynierskiej i akcencie położonym przede wszystkim na wykorzystanie jej wyników do oceny stanu technicznego maszyn i urządzeń oraz optymalizacji gospodarki olejowej. Podejmowane działania mają umożliwić podejmowanie racjonalnych decyzji biznesowych ukierunkowanych na obniżenie kosztów utrzymania ruchu, eliminację przestojów nieplanowych oraz zwiększenie dyspozycyjności urządzeń i instalacji produkcyjnych.
Problematyka związana z badaniami oleju prowadzonymi periodycznie przez pobieranie próbek oleju (płynu hydraulicznego) i badanie ich przez dedykowane laboratoria olejowe nie będzie poruszana.
Planowane są następujące artykuły:
- Wprowadzenie – miejsce diagnostyki olejowej w strategii predykcyjnej utrzymania ruchu opartej o monitoring i ocenę stanu (CBM – Condition-Based Maintenance)
- Parametry oceny stanu układu tribologicznego
- Narzędzia do ciągłego pomiaru stanu oleju i maszyn
- Aplikacje przemysłowe – wybrane przykłady
Cz.1 – Wprowadzenie – miejsce diagnostyki olejowej w strategii predykcyjnej utrzymania ruchu opartej o monitoring i ocenę stanu (CBM – Condition-Based Maintenance)
Monitorowanie i ocena stanu technicznego maszyn i urządzeń
Monitorowanie stanu (Condition Monitoring) to proces monitorowania parametrów stanu maszyn prowadzony w celu wykrywania symptomów mogących pojawić się usterek oraz, jeśli usterki zostaną wykryte, śledzenia ich rozwoju w czasie. Monitorowanie stanu jest głównym elementem konserwacji predykcyjnej (Predictive Maintenance), która jest zdecydowanie bardziej wydajna niż konserwacja prewencyjna (oparta o harmonogram przeglądów), czy reaktywna.
Monitorowanie stanu pozwala na racjonalne planowanie konserwacji (wtedy, gdy jest niezbędna i technicznie uzasadniona) lub podjęcie innych działań w celu eliminacji przestojów nieplanowych, zapobieżenia szkodom wtórnym i uniknięcia ich konsekwencji.
Dodatkowo, skracając przestoje maszyn (planowe i nieplanowe), oszczędzamy pieniądze związane z utrzymaniem ruchu, generujemy dodatkowe zyski ze zwiększonej produkcji oraz zmniejszamy koszty inwestycyjne poprzez wydłużenie żywotność maszyny.
Monitorowanie stanu rozpoczyna się od podstawowych przeglądów. Niewielkie zmiany, takie jak nienormalne ciepło lub ciśnienie, dziwne dźwięki, nadmierne wibracje lub nietypowy zapach, często są oznakami, że maszyna nie pracuje normalnie. Istnieje kilka technik monitorowania stanu maszyny, które są wykorzystywane do oceny ich stanu technicznego:
– diagnostyka wibracyjna
– diagnostyka ultradźwiękowa
– diagnostyka termograficzna
– diagnostyka olejowa
– diagnostyka elektryczna
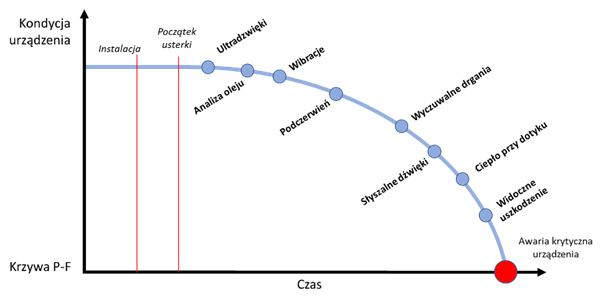
Wybór techniki diagnostycznej zależy oczywiście od rodzaju urządzenia/maszyny, aplikacji, warunków pracy, warunków środowiskowych, dostępności maszyny i wielu innych czynników, ale także od przewidywanej skuteczności działania wybranej techniki z punktu widzenia postawionego celu.
Na rysunku powyżej przedstawiono krzywą rozwoju uszkodzenia maszyny w czasie oraz przewidywaną skuteczność technik diagnostycznych wykorzystywanych do monitorowania jej stanu. Okazuje się, że jedną z bardziej skutecznych technik monitorowania stanu urządzeń informującą o potencjalnym uszkodzeniu maszyny na bardzo wczesnym etapie jego powstania jest analiza (diagnostyka) olejowa.
Monitoring stanu oleju smarnego i hydraulicznego
Diagnostyka olejowa jest najczęściej prowadzona w laboratoriach, w których analizie poddaje się uprzednio pobrane i dostarczone próbki. Testy laboratoryjne są ukierunkowane przede wszystkim na określenie stanu środka smarnego (parametry fizyko-chemiczne, jak lepkość, zasadowość, obecność zanieczyszczeń, wody itp.) i ocena jego przydatności pod kątem dalszego użytkowania lub konieczności wymiany. Jednocześnie technologia ta jest bardzo rzadko wykorzystywana do oceny stanu maszyny (urządzenia), w którym pracuje badany olej.
Duże zmiany w zakresie sposobu prowadzenia diagnostyki olejowej i wykorzystywania jej wyników wprowadziły rozwiązania należące do tzw. Przemysłu 4.0. W dzisiejszych czasach postęp technologiczny umożliwił zastosowanie rozwiązań, dzięki którym możemy monitorować nie tylko stan środków smarnych w czasie rzeczywistym, aby w optymalnym momencie podejmować decyzje o ich wymianie, ale także stopień degradacji powierzchni w krytycznych maszynach, aby przewidywać awarie mechaniczne z dużym wyprzedzeniem.
Miejsce tribologii w monitorowaniu i ocenie stanu technicznego maszyn mechanicznych
Trzy zjawiska mające wydatny wpływ na degradację współpracujących ze sobą ruchomych powierzchni – tarcie, zużycie i smarowanie – bada nauka zwana tribologią. Kiedy maszyny się zużywają, działają gorzej, są mniej wydajne, a w końcu zaczynają ulegać awariom w wyniku uszkodzeń mechanicznych.
Opis procesów powodujących utratę funkcji użytkowych przez maszyny przedstawia poniższy schemat.
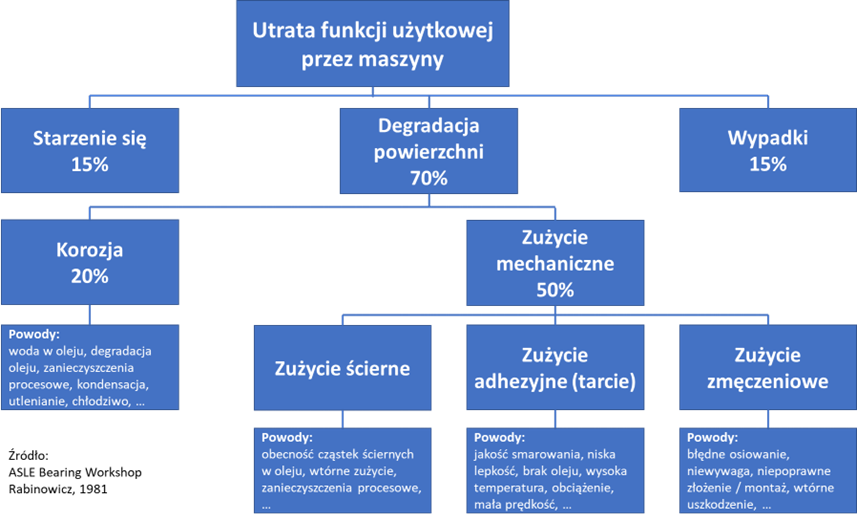
Zużycie zmęczeniowe – Fatigue Wear
Zużycie zmęczeniowe jest rodzajem zużycia, które występuje po wielu cyklach pracy z dużych obciążeń przyłożonym do powierzchni metalowych. Powtarzające się obciążenia powodują mikropęknięcia na powierzchni (lub w podłożu, które mogą rozszerzyć się na powierzchnię), co skutkuje wyeliminowaniem kawałka metalu z powierzchni. Ten tryb zużycia występuje w stykach tribologicznych przy dużych obciążeniach i uszkodzeniach powierzchni, które mogą wystąpić w późnym okresie eksploatacji.
Degradacja powierzchni maszyn, której przyczyną jest zmęczenie materiału, powoduje awarie maszyn w 17% przypadków.

Zjawiska występujące w procesach zmęczeniowych:
Wżery powierzchniowe (Pitting)
Mogą być spowodowane warunkami przeciążenia na powierzchniach współpracujących elementów. Delikatne wżery mogą powodować efekt polerowania na powierzchni, poprawiając wygląd materiałów. Poważne wżery mogą być bardzo destrukcyjne, a ciągłe cykliczne naprężenia powodują znaczne uszkodzenia.
Odpryski (Spalling)
Proces, który może wynikać z poważnych wżerów, które mogą się łączyć, powodując odrywanie większych części materiału.
Kontakt toczny (Rolling contact)
Proces zmęczenia spowodowany uszkodzeniem materiału w wyniku kontaktu tocznego. Może to powodować propagację pęknięć z obszarów naprzemiennych naprężeń powstających w pobliżu powierzchni i prowadzić do pękania elementów.
Zacieranie (Scuffing)
Chociaż zjawisko zacierania nie jest to bezpośrednio związane ze zmęczeniem materiału, może często występować na wczesnych etapach życia elementu, którego powierzchnia jest nierówna w wyniku złej jakości obróbki i wykończenia. Przy utrzymywaniu prawidłowego smarowania i temperatur roboczych zjawisko to zwykle ustępuje i powierzchnie się wygładzają.
Zużycie adhezyjne (ślizgowe) – Sliding Wear
Kiedy dwie obciążone powierzchnie ślizgają się po sobie, generowane siły kontaktowe mogą być wystarczająco silne, aby wystąpiła adhezja (przyleganie – łączenie się ze sobą powierzchniowych warstw ciał fizycznych lub faz). Adhezja spowoduje przeniesienie materiału z jednej powierzchni elementu na drugą. W miarę postępu zjawiska ślizgania, połączenia adhezyjne mogą pękać, tworząc nowe i powodując gromadzenie się zanieczyszczeń.
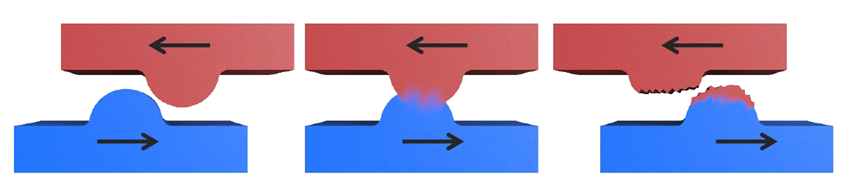
Zużycie adhezyjne można zminimalizować, utrzymując właściwości smarne oleju i stosując wysokiej jakości komponenty z powierzchniami utwardzanymi dyfuzyjnie i o niskim współczynniku tarcia.
Badania wskazują, że degradacja powierzchni maszyn na skutek wystąpienia w nich zjawiska adhezji jest przyczyną awarii maszyn w 13% przypadków.
Zużycie ścierne (ścinające) – Cutting Wear
Zużycie ścierne to rodzaj zużycia, w którym zanieczyszczenia cząsteczkowe i chropowatość powierzchni powodują nacięcia i uszkodzenia na styku powierzchni poruszających się względem siebie. Mechanizm zużycia wynika z bezpośredniego kontaktu twardszego materiału z ruchomymi powierzchniami.
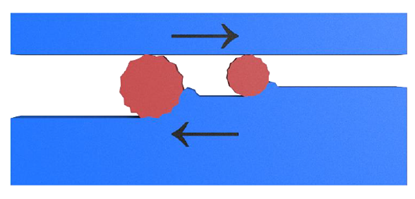
Również podczas pękania połączeń adhezyjnych powstają fragmenty zużywające się. Fragmenty te mogą następnie utleniać się, tworząc znacznie twardsze cząsteczki tlenku, które mogą przedrzeć się przez powierzchnię ślizgową, powodując poważne zużycie ścierne.
Zużycie ścierne nie zawsze może być wynikiem pękania spowodowanego zużyciem adhezyjnym, ale może wynikać z przedostawania się zanieczyszczeń zewnętrznych do układu.
Zużyciu ściernemu można najlepiej przeciwdziałać utrzymując w układzie skuteczny system filtracji.
Zużycie ścierne jest głównym powodem awarii maszyn i ma miejsce aż w 46% przypadków.
Zużycie korozyjne – Corrosion Wear
W przypadku zużycia korozyjnego stan płynu smarującego jest jednym z krytycznych elementów mogących prowadzić do tego typu zużycia. Celem zapobiegania korozji powierzchni jest sprawdzanie kwasowości płynu i zanieczyszczenia innymi płynami, które mogą znacznie zmieniać kwasowość środka smarnego. Przyspieszone utlenianie środka smarnego powoduje zakwaszenie, a także obecność wody i tlenków, które działają jak katalizatory.
Zużycie korozyjne może być również spowodowane oddziaływaniem miejscowym, spowodowanym niektórymi dodatkami w smarze, gdy aplikacja, do której jest używany, nie jest odpowiednia. Z tego powodu ważne jest, aby dostosować użycie smaru i sprawdzić zawartość dodatków zapobiegających korozji związanej z tymi elementami.
Zużycie korozyjne odpowiada za degradację powierzchni maszyn w 9% przypadków ich awarii.
Ocena stanu technicznego systemu tribologicznego
Kontrolowanie warunków, które wpływają na zachowanie systemu tribologicznego (czyli maszyny i środka smarnego jako całości), ma ogromne znaczenie dla ochrony krytycznego sprzętu. Opierając się na wiedzy z dziedzin technologii materiałowej, fizyki i chemii, tribologia jest dziedziną prawdziwie multidyscyplinarną, która wydatnie wspiera wydłużanie żywotności maszyn, skrócenie ich przestojów oraz zwiększenie produktywności.
Aby zapewnić zgodne z oczekiwaniami zachowanie układu tribologicznego, należy ocenić trzy jego podstawowe parametry:
– degradację środka smarnego
– zanieczyszczenie układu tribologicznego
– zużycie maszyny
Monitorowanie wszystkich wyżej wymienionych elementów urządzeń smarowanych olejem jest jedną z najlepszych praktyk tribologicznych. Stopień krytyczności i rodzaj monitorowanych maszyn określi, czy wystarczające będzie prowadzenie regularnych periodycznych analiz, czy też należy zastosować innowacyjne technologie monitorowania ciągłego. Dostępne obecnie na rynku czujniki o działaniu ciągłym mogą być stosowane do pomiaru krytycznych parametrów jakościowych olejów smarowych oraz do generowania wskaźników opisujących stan techniczny maszyn, w których oleje są stosowane.
Artykuł częściowo oparty o materiały firmy ATTEN2.