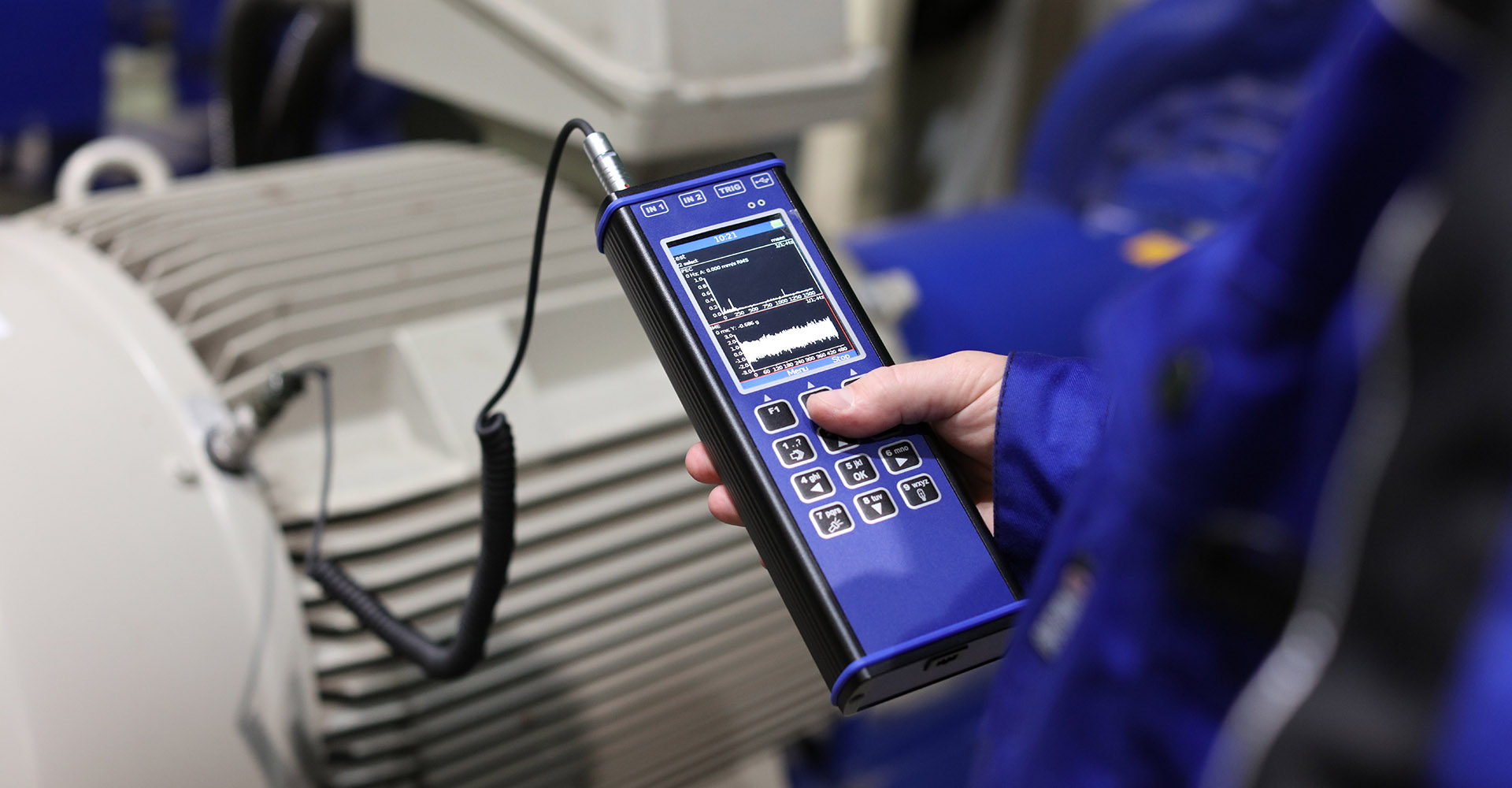
Calibration of measuring devices
Calibration is the process of comparing the measurements made by a device to known standards in order to determine its accuracy and correct any errors. It is an important step in ensuring the reliability and accuracy of measurement data.
Calibration involves comparing the output of the device being calibrated with the output of a reference standard or a calibration standard. The results of this comparison are used to determine any errors in the measurements made by the device and to adjust its readings accordingly.
Calibration can be performed on a wide range of devices, including measuring instruments, sensors, gauges, and meters. It is typically carried out by trained technicians or calibration laboratories that have the necessary equipment and expertise.
The frequency of calibration depends on several factors, such as the type of device, its intended use, and environmental conditions. In some cases, regulatory requirements or industry standards may specify the frequency of calibration. In other cases, the frequency of calibration may be determined based on the manufacturer’s recommendations or the results of previous calibrations.
In summary, calibration is an essential process for ensuring the accuracy and reliability of measurement data. It involves comparing the output of a device with a known standard and adjusting its readings as necessary. The frequency of calibration depends on several factors and should be determined based on the device’s intended use and environmental conditions.
Why calibrate?
Calibration is important for several reasons. First and foremost, calibration ensures that the measurements made by a device are accurate and reliable. This is particularly important in fields such as science, engineering, and manufacturing, where precise measurements are essential for ensuring quality and safety.
Calibration also helps to identify any errors or drift in a device’s performance over time. By detecting and correcting these errors, calibration can help to extend the life of a device and prevent costly downtime or equipment failures.
Furthermore, calibration can help to ensure compliance with regulatory requirements and industry standards. Many regulatory bodies require that certain types of equipment be calibrated at specific intervals to ensure that they are functioning properly and providing accurate measurements.
Finally, calibration can help to improve the overall efficiency of a process or system by reducing waste, improving product quality, and increasing productivity. By ensuring that devices are measuring accurately and consistently, calibration can help to identify areas for improvement and optimize processes.
In summary, calibration is important because it ensures accuracy and reliability, detects errors and drift, ensures compliance with regulatory requirements, and improves efficiency.
Who can perform calibration of measuring devices?
Calibration of measuring devices should be performed by trained and qualified personnel or by a certified calibration laboratory.
In general, calibration requires specialized knowledge and skills, as well as access to calibration standards and equipment. Therefore, it is important that individuals or organizations performing calibration have the necessary training, experience, and resources to perform the work correctly.
Some manufacturers provide calibration services for their own devices. However, independent calibration laboratories can also perform calibration services for a wide range of devices from various manufacturers.
In many cases, calibration laboratories are accredited by national or international accreditation bodies, such as ISO/IEC 17025, to ensure that they meet strict standards for technical competence and quality management. Accreditation provides assurance that the laboratory has been independently evaluated and is capable of performing accurate and reliable calibrations.
In summary, calibration of measuring devices should be performed by trained and qualified personnel or by certified calibration laboratories that have the necessary knowledge, skills, and resources to perform the work correctly. Accreditation by a recognized accreditation body can provide additional assurance of technical competence and quality management.
What is an accredited calibration?
An accredited calibration is a calibration performed by a calibration laboratory that has been accredited by an independent accreditation body to comply with international standards for testing and calibration laboratories, such as ISO/IEC 17025.
Accreditation is a formal recognition that a calibration laboratory has demonstrated technical competence and has implemented a quality management system that meets international standards. Accreditation involves an evaluation process conducted by an independent accrediting body to assess the laboratory’s technical competency, quality management system, and proficiency testing program.
An accredited calibration provides a high level of assurance that the calibration results are accurate and reliable. Accreditation also ensures that the calibration laboratory has the necessary equipment, personnel, procedures, and processes to perform calibrations according to the highest international standards.
Accreditation is important for many reasons. For example, regulatory bodies may require that calibrations be performed by accredited laboratories to ensure compliance with regulations. Additionally, many industries, such as aerospace, automotive, and medical device manufacturing, require that measuring devices be calibrated by accredited laboratories to ensure product quality and safety.
In summary, an accredited calibration is a calibration performed by a calibration laboratory that has been independently accredited to comply with international standards for testing and calibration laboratories. Accreditation provides assurance that the calibration results are accurate and reliable and that the laboratory has the necessary equipment, personnel, procedures, and processes to perform calibrations according to the highest international standards.
How often do I need to calibrate the measuring instruments (calibration cycle, calibration interval)?
The frequency of calibration, or the calibration cycle/interval, depends on several factors such as the type of instrument, its intended use, and the environmental conditions it is exposed to. The calibration interval should be determined based on the manufacturer’s recommendations, industry standards, regulatory requirements, and the results of previous calibrations.
Many manufacturers provide recommendations for the calibration interval of their instruments based on their design, specifications, and usage. Industry standards, such as those developed by organizations like the National Institute of Standards and Technology (NIST) or the International Organization for Standardization (ISO), may also provide guidance on the frequency of calibration for specific types of instruments.
Regulatory requirements may also mandate specific calibration intervals for certain types of instruments, especially those used in critical applications such as medical, pharmaceutical, or aerospace industries.
The results of previous calibrations may also be used to determine the appropriate calibration interval for an instrument. For example, if an instrument shows significant drift or measurement errors during a calibration, it may be necessary to shorten the calibration interval to ensure that it remains within its specified accuracy range.
In summary, the calibration cycle or interval should be determined based on the manufacturer’s recommendations, industry standards, regulatory requirements, and the results of previous calibrations. It is important to follow the recommended calibration interval to ensure that the instrument remains accurate and reliable, and to avoid potential measurement errors or inaccuracies.
We offer a wide range of calibration of vibration meters and analyzers.
Feel free to contact us: info@vims.pl