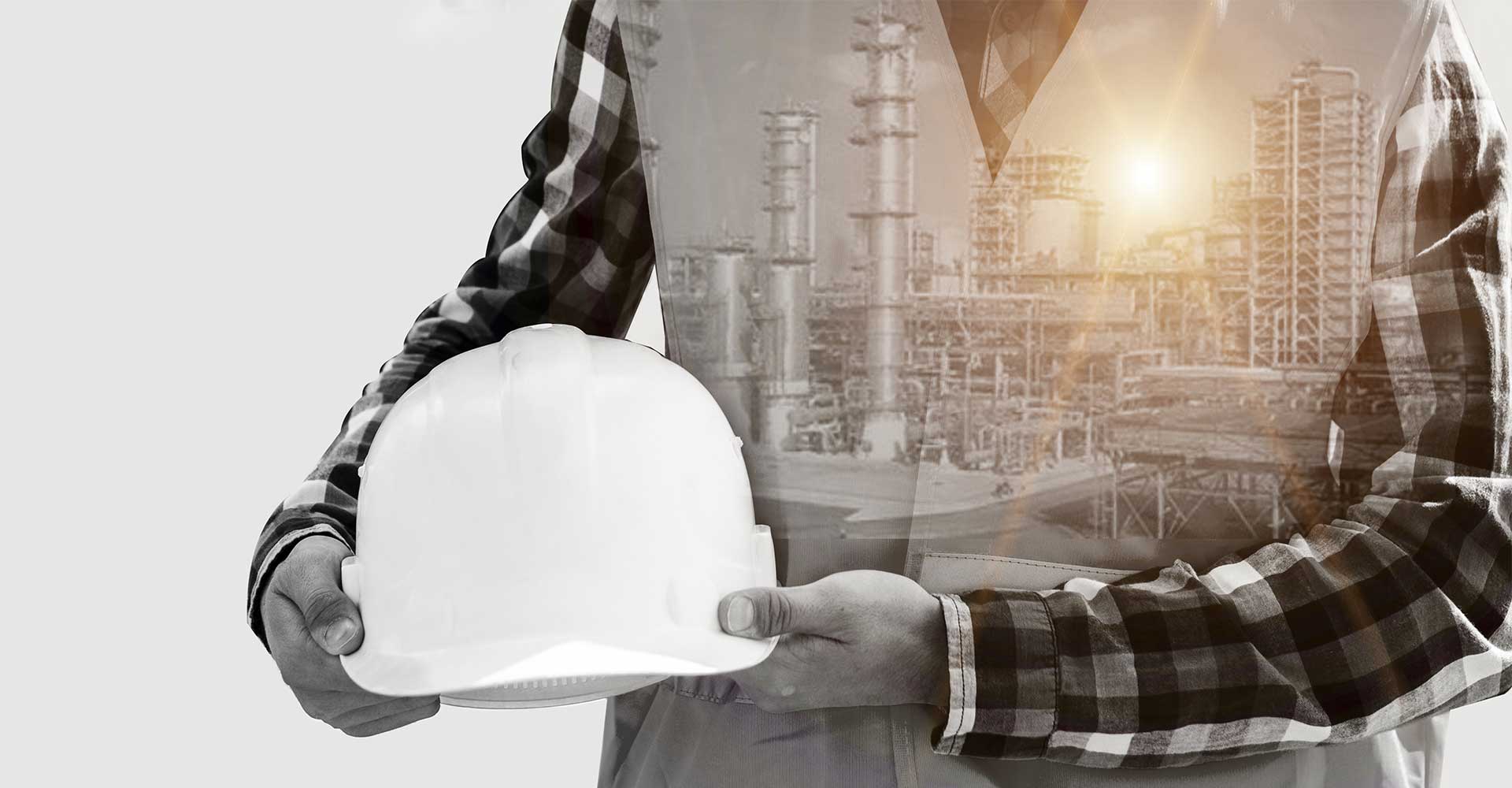
Maintenance – definition, types and application
Learn about the different types of maintenance and how each industry benefits from good maintenance practices.
What is maintenance?
Maintenance, otherwise known as upkeep, refers to a set of processes and practices designed to ensure the continuous and efficient operation of machinery and facilities. Diligence in implementing an effective maintenance program is essential to the successful operation and longevity of machines, assets, facilities and entire companies.
The main objectives of maintenance are:
The main objectives of maintenance are:
- Ensuring reliability and availability: Maintenance aims to minimize breakdowns and downtime in production or service operations through regular maintenance, repair and condition monitoring of equipment.
- Optimizing costs: By planning and executing maintenance and repair work at the right times, maintenance costs can be minimized and costly emergency repairs avoided.
- Productivity and efficiency: By ensuring that assets are maintained in good working order, organizations can achieve better efficiency in production processes or service delivery.
- Safety: Ensuring that machinery and equipment are in safe working condition is key to preventing accidents and hazards to employees.
- Extending useful life: Adequate maintenance can extend the useful life of equipment and machinery, which translates into savings and increased return on investment.
The most common types of Maintenance
There are different types of maintenance work, each designed for specific scenarios. Knowing the differences between maintenance types helps determine which is most appropriate to achieve the goal.
In practice, industrial plants use one of three maintenance strategies: reactive, preventive, predictive or proactive, or possibly a combination of them.
Reactive maintenance
Reactive maintenance is an approach to managing and maintaining equipment and infrastructure that focuses on responding quickly to failures, disruptions, or other unforeseen problems. It is particularly important for systems, machinery, industrial equipment, or critical infrastructure, where downtime or failures can lead to significant financial losses or safety risks.
The main features of reactive maintenance are:
- Diagnosis and repair of failures: Reactive maintenance involves quickly identifying the cause of failures or disruptions and repairing them. This may require access to specialized technical personnel and often uses diagnostic tools.
- Condition monitoring: Reactive maintenance systems often use a variety of sensors and monitoring tools to track the condition of equipment and infrastructure in real time. This allows for rapid response to irregularities.
- Scheduling inspections and maintenance: Although the reactive approach involves repairing after a problem occurs, there is also a need for regular inspection and maintenance to reduce the risk of failure.
- Documentation: An important part of reactive maintenance is keeping records of failures, repairs, inspections and other maintenance activities. This helps in long-term analysis and in improving the maintenance process.
It is worth noting, however, that reactive maintenance is not an ideal approach to asset management. More advanced maintenance strategies, such as preventive (predictive) and predictive maintenance, avoid failures and downtime by scheduling inspections and maintenance based on equipment condition data and its projected life. This can minimize failure and maintenance costs and increase system availability and performance.
Preventive maintenance
Preventive Maintenance (PM) is a maintenance management strategy that relies on planned and regular maintenance activities and inspections to prevent breakdowns and keep equipment and infrastructure in the best possible condition. The main goal of preventive maintenance is to minimize downtime, extend the life of equipment and reduce the cost of repairs and emergency interventions.
Here are some key features of preventive maintenance:
- Regular maintenance: Scheduled and regular maintenance of equipment is carried out on schedule, regardless of its condition. This helps detect early signs of wear or potential problems before they become major failures.
- Preventive maintenance: The PM strategy also includes regular maintenance activities such as lubrication, cleaning, adjustments and calibrations to help keep equipment in optimal condition.
- Planning and scheduling: Preventive work is planned in advance and scheduled at convenient times to minimize disruption to production or operations.
- Documentation: All preventive work and inspections are accurately documented. This allows maintenance history to be tracked and strategy to be adjusted based on the data collected.
- Data analysis: Preventive maintenance uses equipment condition data, such as technical parameters, inspection results and analysis, to assess the condition of equipment and forecast when to replace or upgrade.
- Staff training: An important aspect is that personnel are properly trained to perform inspections and maintenance, which helps ensure that these activities are performed correctly.
Preventive maintenance has many advantages, such as increased equipment reliability, reduced repair and downtime costs, and optimal use of resources. However, it requires proper planning, supervision and documentation to achieve its full effects. As technology evolves, condition monitoring tools and systems can also be used to further enhance preventive maintenance through predictive maintenance activities.
Predictive maintenance
Predictive Maintenance (PdM) is an advanced maintenance management strategy that relies on the use of data, sensors and predictive analytics to anticipate equipment and infrastructure failures and maintenance needs. The main goal of predictive maintenance is to minimize downtime, reduce maintenance and repair costs, and increase system availability and performance.
Key elements of predictive maintenance:
- Condition monitoring: Sensors and monitoring tools are used to continuously collect data on the condition of equipment, such as technical parameters, vibration, temperatures, wear levels, etc.
- Data analysis: Data collected from sensors is analyzed using advanced techniques such as statistical analysis, machine learning and artificial intelligence. This analysis identifies patterns, trends and anomalies in the data that may indicate an impending failure.
- Failure forecasting: Based on data analysis, it is possible to predict when equipment or components will require maintenance or repair. This enables you to plan actions before a failure occurs, minimizing downtime and costs.
- Maintenance scheduling: Maintenance activities are scheduled based on forecasts and priorities, allowing optimal use of resources and minimizing production disruption.
- Staff training: Personnel responsible for operating and maintaining equipment must be properly trained in the use of monitoring and data analysis systems.
- Documentation: All activities and data analysis results are accurately documented, allowing maintenance history to be tracked and strategies to be refined based on the data collected.
Predictive maintenance has many advantages, including increasing equipment reliability, minimizing maintenance costs, improving operational safety and increasing production efficiency. This is especially important for critical infrastructure and advanced industrial systems. By accurately predicting failures, downtime and repairs can be avoided in situations that can be costly or endanger people.
Proactive maintenance
Proactive Maintenance or PM is an approach to managing the maintenance of equipment or infrastructure. It aims to prevent failures and maximize performance through regular maintenance, diagnostic and repair activities. Unlike reactive maintenance, which involves repairing equipment after it fails, proactive maintenance relies on planned interventions and damage prevention.
The main features of proactive maintenance are:
- Planning and scheduling: Regularly scheduled maintenance and inspection activities that take place at specified intervals prevent sudden failures.
- Diagnostics: Using advanced diagnostic tools such as sensors to monitor equipment condition, data analysis, thermal imaging, and vibration diagnostics to detect potential problems and equipment malfunctions before failure occurs.
- Preventive maintenance: Performing regular maintenance such as lubrication, cleaning, calibration and replacement of worn parts to keep equipment in optimal condition.
- Personnel training: Ensuring that maintenance personnel are properly trained so that they are able to effectively perform proactive activities.
- Data analysis and statistics: Using historical data analysis and statistics to identify failure trends and improve the proactive maintenance strategy.
- Quality control: Regularly inspecting the quality of processes and products to detect problems that may affect equipment health.
- Technology innovation: Implementing new technologies such as the Internet of Things (IoT), artificial intelligence (AI) and machine learning to automatically monitor and manage equipment.
Proactive maintenance is designed to minimize production downtime, improve occupational safety and productivity, and reduce the cost of repairs after failures. It is an important strategy in many industries, such as manufacturing, chemicals, energy, transportation and many others, where malfunctioning equipment can lead to significant financial losses and risks to the health and lives of workers.
Maintenance, and industrial sectors
Maintenance plays a key role in industry, where it is widely used. Here are some examples of its applications in various industries:
- Manufacturing industry: In factories and production facilities, maintenance is essential to ensure continuous production. Through regular inspection and maintenance of machinery and production systems, downtime, breakdowns and production costs can be minimized. Monitoring the condition of equipment and predicting failures can also increase production efficiency and quality.
- Power Generation: In the energy sector, in both conventional and renewable power plants, maintenance is key to maintaining a continuous energy supply. Maintenance of turbines, generators, transmission and distribution facilities helps avoid breakdowns and outages.
- Chemical industry: In the chemical industry, where many chemical processes and large-scale operations take place, maintenance of equipment and facilities is essential for reasons of safety, environmental protection and production efficiency.
- Petrochemical industry: In this industry, maintenance of pipelines, tanks, reactors and other equipment is vital because of the risk of leaks and failures that can lead to environmental disasters and risks to workers.
- Aerospace: In the aerospace sector, where safety is a priority, maintenance is critical to ensuring the operability of aircraft, missiles and aerospace infrastructure.
- Automotive: In the production of automobiles and other vehicles, maintenance minimizes line failures and ensures vehicle quality and safety.
- Food industry: In the food industry, where hygiene and product quality are a priority, maintenance is crucial to ensure the reliability of production machinery, packaging and food storage equipment.
- Pharmaceutical industry: In the production of drugs and other pharmaceutical products, maintenance is essential to comply with strict regulatory standards and ensure patient safety.
- Transportation and logistics: In the transportation sector, management of vehicle fleets and transportation infrastructure requires maintenance to ensure reliability and safe travel.
- Urban infrastructure: In cities and urban areas, maintenance is critical to the operation of water, sewage, electricity, lighting, transportation and other infrastructure systems.
These are just a few examples of maintenance applications in various industries.
Maintenance is a key element in ensuring the reliability and efficiency of industrial operations and technical infrastructure.