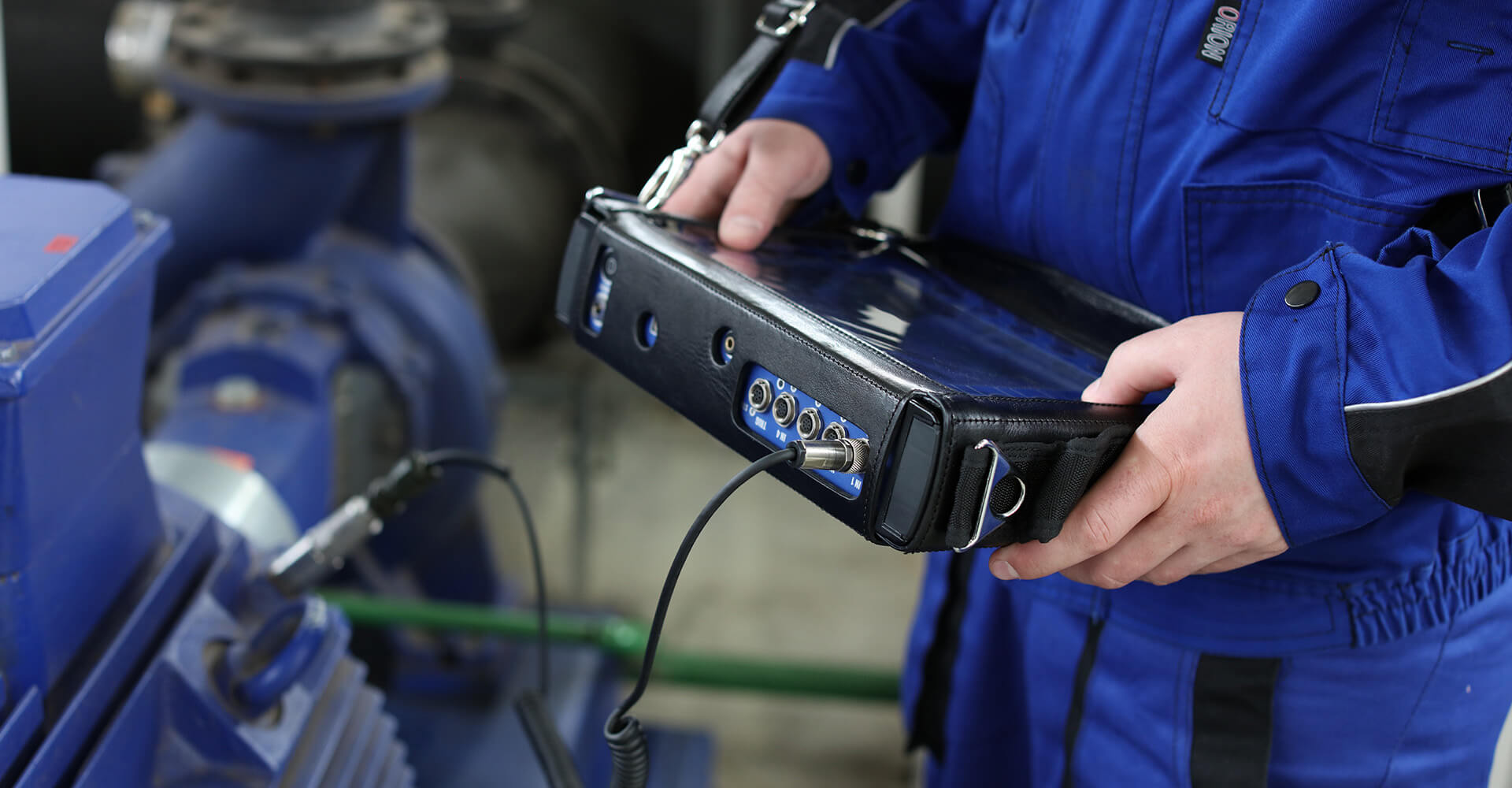
Industrial machinery diagnostics
Machine diagnostics and proper operation are the most important requirements for industrial machinery to ensure smooth production processes. Frequent damage to small components results in significant losses due to unplanned stops in the production process.
Diagnostics of machines and equipment and monitoring of their operating parameters will undoubtedly allow to avoid failures, plan maintenance and overhaul periods and extend the service life.
What is machine diagnostics, where and why should it be used?
WHAT IS INDUSTRIAL MACHINERY DIAGNOSTICS?
Machine diagnostics is a concept that is of great importance. It directly affects the condition of machines, improves the efficiency of machine operation, as well as reduces the costs associated with their operation. Good technical condition of the machinery fleet greatly improves the safety of operators and maintenance workers. Machine diagnostics is supported by various measurement methods, such as ultrasound, thermal imaging, tribology, vibrodiagnostics and electric motor inspection.
MACHINE DIAGNOSTICS – WHERE CAN WE APPLY?
Machine diagnostics are widely used in all industries. From the pharmaceutical industry and FMCG production lines, where product sterility is crucial, through automotive industry machines and production lines in which the focus is on precise manufacturing of the finished product, to heavy industry factories such as refineries, mines, power plants and steel mills, where machines work with heavy loads and media supply systems must deliver raw material over long distances. Undoubtedly, a properly selected measurement method allows the user to rest easy, without worrying about unexpected failures.
WHAT OBJECTS CAN WE CONTROL?
The choice of measurement method depends on the type of object being measured and the type of potential damage we will diagnose. With the help of modern technology, we inspect the tightness of compressed air (or other special gases) installations, test the operation of fans, pumps, presses, compressors and complex drives to verify their technical condition. We also check the electrical connections of control cabinets to prevent surges and monitor the operation of electric motors for proper functioning.
WHO CAN USE?
The possibilities for equipment are endless. Portable devices are available for diagnosticians who want to take measurements directly at the equipment or plant. There is also the possibility of permanent monitoring of machines where access is limited or which operate in hazardous conditions. Therefore, we use online measurement methods. Measurement sensors are permanently mounted on the monitored systems, and the results are sent to stationary units. An important aspect is the proper installation of the sensors.
We offer advice on the selection of measurement technology for the needs of machines and entire installations that users have. Feel free to contact us: info@vims.pl
BENEFITS OF MACHINE DIAGNOSTICS
By testing your industrial machines, you will undoubtedly identify design errors at an early stage and avoid risks, costs and failures.
By monitoring the operating status of machines, you can:
eliminate sudden machine shutdowns due to breakdowns;
reduce expenditures from raw material takeoffs;
control the stock of spare parts;
precisely organize the activities of DUR employees;
increase the safety of employees;
increase the efficiency of machines.