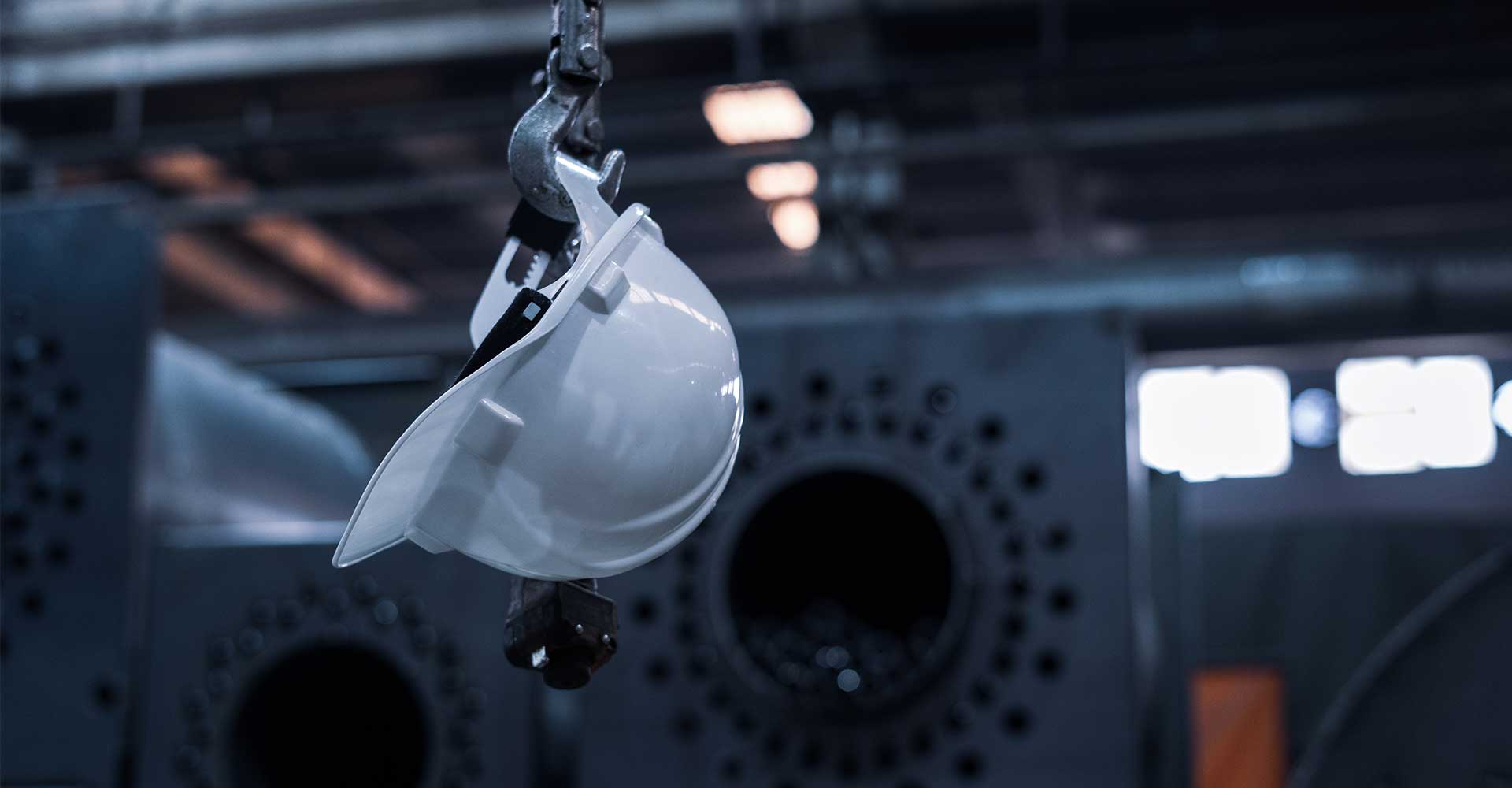
Technical diagnostics for machinery – Types
Technical diagnostics for machinery refers to the process of analyzing the technical condition of machines and equipment in order to detect, identify and assess any abnormalities and predict future breakdowns.
The goal of technical diagnostics is to prevent breakdowns, minimize downtime and increase the efficiency and reliability of machines and equipment.
Technical diagnostics can involve different methods, such as vibration diagnostics, thermographic diagnostics, oil analysis, visual diagnostics, acoustic diagnostics, electrical diagnostics, and process diagnostics.
In the process of technical diagnostics, data is first collected about the machines, including information about their construction, technical specifications, usage history, etc. Then, using appropriate diagnostic tools, tests are conducted to examine the technical condition of the machines. This data is then analyzed and interpreted by experts who make decisions about repairs and maintenance of the machines.
Technical diagnostics for machinery is important in many fields, including industry, transportation, energy, production, and many others. It enables the prevention of breakdowns, minimizes downtime and repair costs, and increases the efficiency and reliability of machines and equipment.
Machine diagnostics are important for several reasons:
- Preventive maintenance: Diagnostics can help identify potential problems before they become serious issues. This allows for preventive maintenance to be scheduled to prevent unplanned downtime and reduce repair costs.
- Improved efficiency: Machine diagnostics can identify areas where machines are operating less efficiently than they could be. By addressing these issues, productivity can be increased, energy consumption reduced, and overall efficiency improved.
- Safety: Diagnostics can help identify potential safety hazards, such as worn or damaged parts, that could lead to accidents. By addressing these issues, the risk of accidents can be reduced, and workplace safety can be improved.
- Cost savings: By identifying potential problems early, repairs can be scheduled before they become major issues, which can save time and money. In addition, improved efficiency can result in energy savings, reducing operating costs.
- Machine lifespan: Regular machine diagnostics and maintenance can help extend the lifespan of machines, reducing the need for replacement and associated costs.
In summary, machine diagnostics are important because they help prevent unplanned downtime, improve efficiency, promote safety, save costs, and extend machine lifespan.
Types of technical diagnostics for machinery
There are various types of technical diagnostics for machinery, including:
- Vibration diagnostics: This method involves measuring and analyzing vibrations in the machinery to detect any potential problems or abnormalities in its operation.
- Thermographic diagnostics: This method uses thermal imaging cameras to detect any changes in temperature, which can indicate overheating or other issues.
- Oil analysis: By analyzing the oil in a machine, technicians can detect any contaminants, wear metals, or other indicators of potential problems.
- Visual diagnostics: This method involves a visual inspection of the machinery to identify any obvious signs of damage, wear and tear, or other issues.
- Acoustic diagnostics: This method involves measuring and analyzing sound waves to detect any potential problems, such as bearing wear, gear misalignment, or other mechanical issues.
- Electrical diagnostics: This method involves testing the electrical systems of the machinery to detect any issues with voltage, current, or other electrical parameters.
- Process diagnostics: This method involves analyzing the entire process in which the machinery is involved, including input materials, process parameters, and output products, to detect any potential problems or inefficiencies.
These are just a few examples of the types of technical diagnostics available for machinery. Depending on the type of machinery and its intended use, other methods may also be used to diagnose potential problems and optimize its operation.